Inspection equipment for the production of automotive headlamps
Camera systems for visual inspection in automated production. The system checks for the presence, correctness of parts and completeness of the product during assembly, and also allows electrical and mechanical tests to be carried out, along with providing quality control of optical parameters.
Automotive headlight production testers used for comprehensive testing of headlights and taillights – checking the functionality of individual lighting functions and their parameters. They also serve as a check when assembling individual headlight parts. In addition to the aforementioned checking of the presence and types or positions of parts, it also checks the faultless execution of assembly.
Typical application
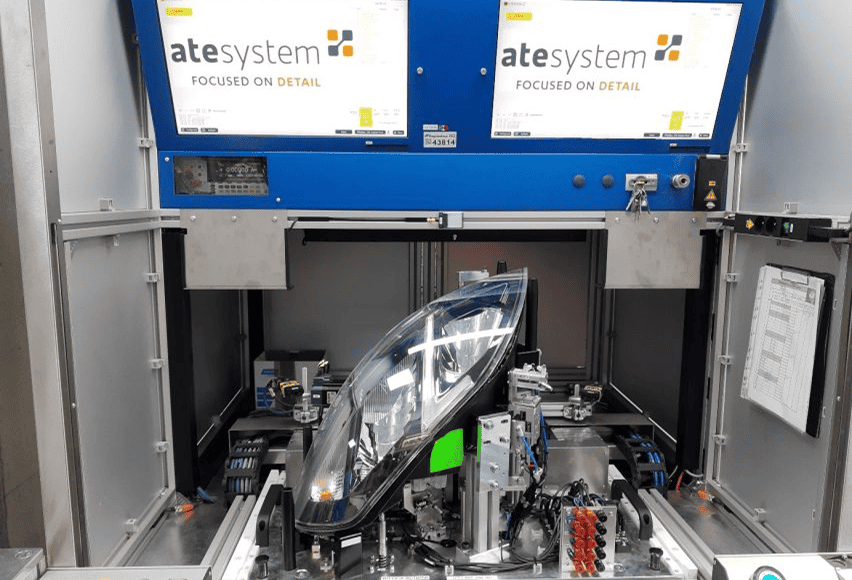
Optional system parameters and possible controls include:
Presence and qualitative tests
- Choice of light source from traditional (incandescent bulb) to modern light sources (xenon lamp, LED, laser).
- Checking the assembly of modules and headlights (checking the presence of parts).
- Checking the presence of the outer (hard coat) and inner (anti-fog) paint on the headlamp cover glass.
- Measurement of headlamp electrical parameters.
Communication
- Communication with external PLC systems.
- Communication with external input and output peripherals, current sources, motors.
- Communication with headlights via CAN and LIN buses.
- Communication with car simulation modules – HSX, Vector, DAP.
Optical and camera tests
- Checking the AFS functions (cornering lights).
- Checking the mechanical functions of the LWR (headlamp height adjustment).
- Checking the ignition of xenon lamps (burn-in test).
- Homogeneity and colour check in XY coordinates.
- Detection of defective LEDs (colour and brightness change).
- Check the swipe function (gradual lighting) of the turn signals with a high-speed camera.
- Check the matrix function (glare reduction for oncoming traffic).
- Lighting of the headlight modules using their own current sources.
Optical-mechanical tests
- Position adjustment and checking of the illumination position of the main headlights of the car.
- Adjusting and checking the lighting of the individual headlamp functions.
- Adjusting and checking the colour of the headlamp projector interface.
- Checking that the headlamp wiring connectors are plugged in using the cameras.
- Check the lens cleanliness of the headlight module using artificial intelligence and deep learning methods.
- Primary optics adjustment.
All optical inspections carried out fully comply with the relevant standards, whether European Union or other international standards. The main advantage of our system is considered by the customer to be its easy adjustability, which is fully open to the end user (operator or technologist) from the application user interface. The end customer is therefore able to create new configurations, set test parameters or make routine changes to limits without the presence of ATEsystem s.r.o. programmers.
The majority of the automatic machines we supply for part adjustment and inspection are built on the ATEster software platform, which is a modular machine vision platform based on the LabVIEW programming environment. The developers of the platform have as their main goal to make it easy, fast and also customizable for machine vision tasks for various industries. It aims to provide the end customer with clear information about vision inspection, the ability to set or parameterize individual tests, and the ability to link to existing industrial technologies.
The app itself offers the following options in its basic form:
- Communication with cameras from multiple manufacturers.
- Easy and quick setup of the product to be manufactured + possibility to specify new products.
- Setting the parameters of the tests to be performed.
- User management.
- Storage of images and production data.
Other application options include:
- Control of mechanical or pneumatic actuators and motors.
- Possibility of connection to internal databases (e.g. MES) or PLC controllers, and thus the possibility of operation in the intelligent sensor mode.
- Creating reports or connecting to the Ministat product (complete database server for data processing and visualization).
- Possibility to connect to artificial intelligence methods.
You don’t know what to do? We will find a tailor-made solution for you.
Do you need to consult a specialist?
Feel free to contact us directly or use the form below.
System Integration Department
Turnkey solution
Free consultation
Let us help you solve your problem. Contact us and take your projects to the next level!
Other solutions
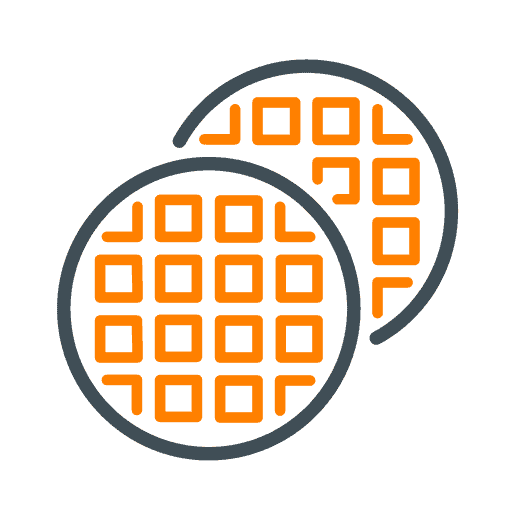
Inspection in the semiconductor industry
We have developed and implemented advanced systems for optical inspection of wafers, prediction of wafer breakage including control of correct wafer seating in lithography.
Machine learning (deep learning) and neural networks
Advanced image analysis using deep learning methods also enables camera inspections in machine vision applications where conventional methods cannot be used.
Checking the application of heat conductive paste and adhesive
Camera systems for quality control of the coating on the base part, on which the electronic part is subsequently deposited. The task is to check the quantity and distribution of the applied paste.